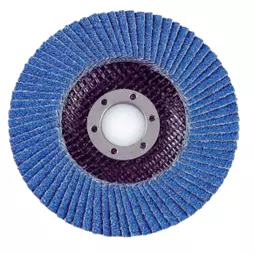
Flap Discs
A flap disc is an abrasive tool used for grinding, blending, and finishing metal, wood, and other materials. It consists of overlapping abrasive flaps arranged in a circular pattern and attached to a central hub. The flaps are typically made from materials like aluminum oxide or zirconia alumina, and they are bonded to a backing plate, which is then mounted on a grinding or angle grinder.
Key Features of Flap Discs:
Versatility: Can be used for grinding, deburring, finishing, and blending.
Abrasive Material: Common materials include aluminum oxide (for general-purpose use) and zirconia alumina (for more aggressive grinding).
Grit Size: Available in various grit sizes, ranging from coarse (e.g., 40-60 grit) for heavy material removal to fine (e.g., 120-240 grit) for finishing and polishing.
Backing Plate: Usually made of fiberglass or plastic, providing durability and flexibility.
Size: Common diameters include 4.5 inches, 5 inches, 7 inches, and 9 inches, with different bore sizes to fit various grinders.
Applications:
Metalworking: Removing weld seams, smoothing rough edges, and blending surfaces.
Woodworking: Sanding and finishing wooden surfaces.
Automotive: Repairing and refinishing car bodies.
Construction: Smoothing concrete or stone surfaces.
Advantages:
Longer Lifespan: The overlapping flaps wear down gradually, exposing fresh abrasive material.
Consistent Finish: Provides a uniform finish compared to traditional grinding wheels.
Reduced Heat Build-Up: The flaps dissipate heat better, reducing the risk of damaging the work piece.
Safety Tips:
Always wear protective gear, including gloves, safety glasses, and a face shield.
Ensure the flap disc is securely attached to the grinder before use.
Use the appropriate grit and type of flap disc for the material and task.
Avoid applying excessive pressure, as this can cause the disc to wear out quickly or damage the work piece.